Sure, composite decking is some of the most durable deck material money can buy, but what makes it so tough? The Deck Supply is always excited to dig into the details. So, let’s peel back the layers of our favorite solutions building the future of modern decks!
Recycled Materials
Some recycled products get a bad rap because people believe they can be low-quality or unreliable. However, composite decking is actually tested to last longer and stay stronger than wood planks! Sustainable solutions don’t always mean sub-par quality. That’s why this ultra-durable deck material is winning over more homeowners than ever before!
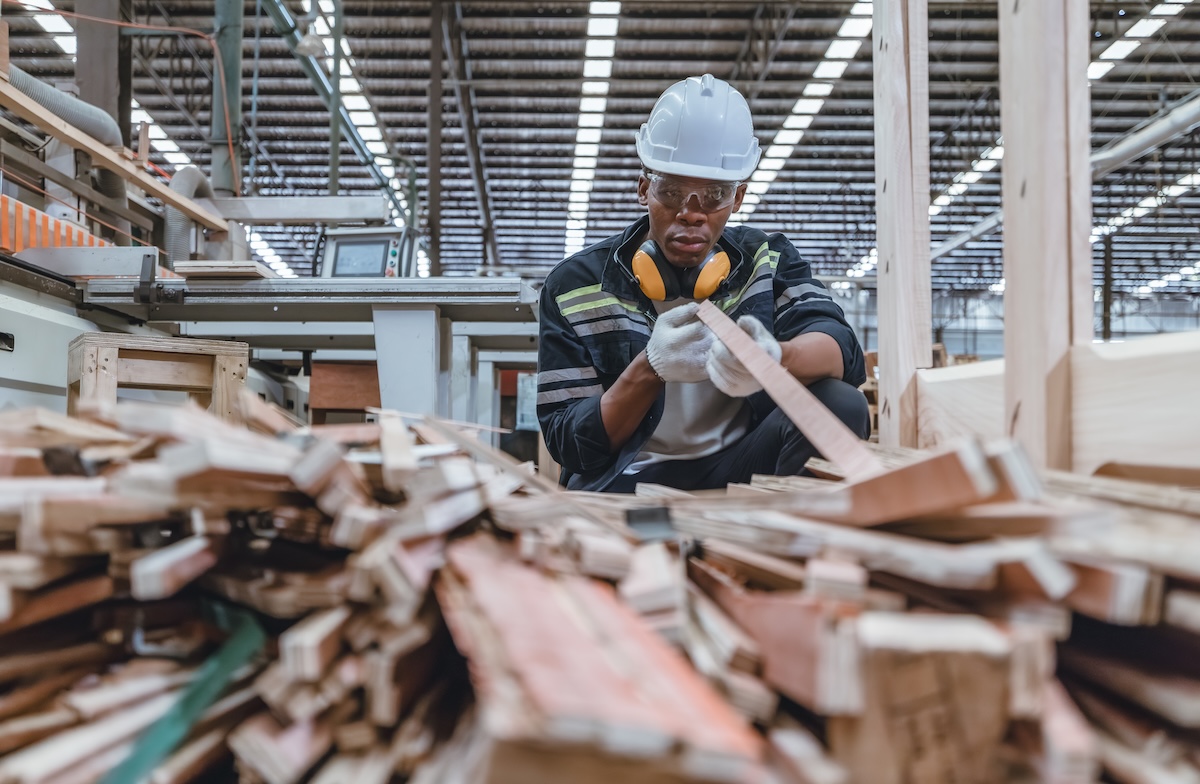
The recycled wood used in composite deck boards is derived from sawdust, wood chips, and other wood fibers. Typical sources for this reclaimed wood are construction sites, furniture manufacturing, and even old decks! By recycling this wood waste, composite boards help to conserve natural resources and reduce landfill waste.
PVC
Plastic is a fantastic material used in many materials around your home. From plumbing to countertops, polyvinyl chloride (PVC) is the most common type of recycled plastic used in construction. PVC is used as a final coat on “capped” composite deck boards. With this cap, composite boards are waterproof, preventing warping, cracks, and splitting.
Bonding Agents
There are a few ways that our suppliers bond wood fibers together in composite boards. In both capped and uncapped boards, there are a few bonding agents used in this durable deck material. High-density polyethylene (HDPE) is a weather-resistant polymer used as the primary binder in composite decking.
These plastic-based bonding agents offer lasting adhesion, flexibility, and impact resistance. Polyurethane (PU) is also used for great adhesion, flexibility, and waterproofing. Epoxy is another high-strength resin used in some premium composite decking for its exceptional bonding power and resistance to moisture. However, epoxy can be more expensive and require specialized handling compared to other polymers.
How It’s Made
Now that you know the basic components of our most durable deck materials, it’s important to understand how they all come together. For this, we’ll look into the two main processes used by Fiberon. This brand uses a combination of recycled and virgin materials to create each board.
The process starts by combining the wood fibers and bonding agents. These materials are heated to create a pulp mixture that can be molded to exact specifications. During this step, the pulp is thoroughly tested to ensure proper blending and forming. With a proper molten pulp, the composite board is ready to take shape!
Molding
Fiberon uses one of two processes to create both uncapped and capped deck boards. In the extrusion process, the mixture is forced through a mold shaped like a deck board. This creates a continuous profile with consistent dimensions throughout the board.
The other process uses a technique referred to as compression molding. This is where the mixture is poured into a mold with patterns and textures. To set these textures, the mold is then compressed under intense heat and pressure to form individual boards.
Finishing
Following these processes, the newly formed boards are set aside to cool down gradually. They are also monitored and measured to ensure stability and prevent warping. To finish the job, additions like embossed wood grain patterns and protective PVC caps offer enhanced durability and a natural look.
Before these durable deck materials are shipped to our showroom, each board undergoes rigorous testing to ensure it meets specific standards. Our suppliers test every board for strength, density, moisture resistance, and other vital properties.
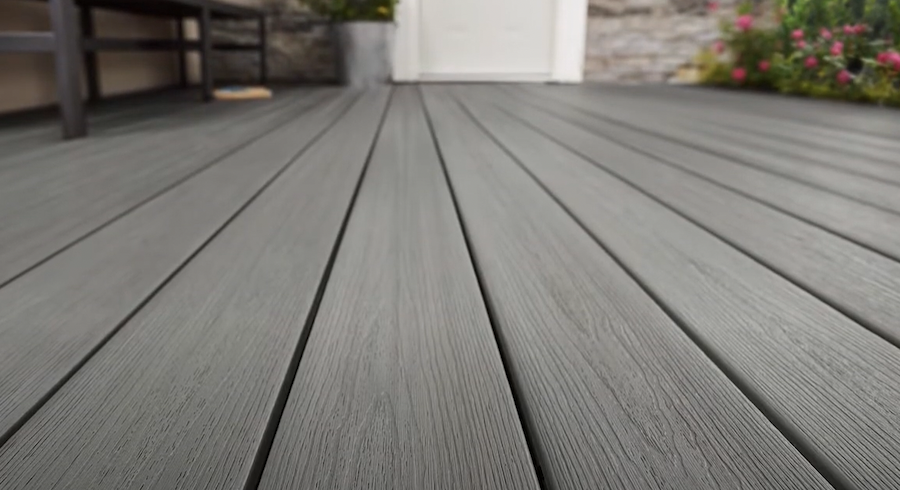
Building Durability With The Deck Supply
Truly durable deck materials are paving the way for sustainable, beautiful decks across the United States. If you’re looking to upgrade your deck or build lasting value from scratch, there’s only one place to go. Request a quote, or give us a call to find the most durable materials on the market!